Press release
Guyson Robot Loaded Shot Peening Automation With Traceability

large automated, robot loaded, twin blast machines, for shot peening turbomachinery turbine blades or medical implants
The system comprises two Guyson Multiblast RXS900 automated blast systems; one for steel shot peening and one for glass bead peening, with robotic work piece transfer between the two blast systems. The computer controlled process was designed to meet AMS2432 standards demanded by the client. This fully integrated process with traceable record keeping delivered increased capacity with less labour compared to the existing process.
Batches of 12 workpieces in a dual indexing carousel for In/Out control are picked up one at a time by an ABB robot and sequenced through the system. Suitable for turbomachinery turbine blades or medical implants, each piece is loaded into the six rotary indexing stations of the Guyson RXS900 (Rotating indeXing Spindle) shot peening system located to its left. The components index clockwise through two shot peening stations - both equipped with two boron carbide blast nozzles, four in total, which vertically stroke up and down the workpiece, delivering the correct Almen intensity, at the correct impingement angle and providing 100% surface coverage.
Steel shot blast media is delivered to the blast nozzles via a 300 litre twin chamber pressure pot, allowing for continuous media flow during the long peening operation. To meet AMS2432 standards media flow rate is monitored and controlled with Magnavalves whilst closed loop peening air pressure, spindle RPM and vertical gun traverse rates are all held within tight specifications. An airwash station, separated by an internal pneumatic vertical door, removes residual dust and blast media from the components prior to removal from the blast machine.
Due to the heavy weight of steel shot used in the peening process, a bucket elevator transfers the used blast media, via Archimedes type auger screw, into the reclamation unit to maintain blast media quality. This unit comprises a 30" 3-deck sieve separator which removes any oversize particulates via the upper decks to a waste bin. Shot that is within size tolerance of the process is returned to the storage hopper via the lower deck. Any particulates deemed smaller than tolerance pass through the decks to a waste bin. An integrated spiral roundness classifier removes up to 10% of the blast media during the reclamation process and removes any mis-shapen shot, before returning good media to the system.
A large reverse jet pulse cleaning dust collection unit provides automated cleaning of the four filter elements during the operation of the blast system, this being particularly beneficial for continuous blast operations. The dust collector is fitted with secondary HEPA14 filter, back-flap valve and explosion relief valve.
Following steel shot peening a de-contamination glass bead peening operation is undertaken. The same ABB robot unloads each station as it exits and transfers components to the glass bead peening system; where bead peening takes place in a similar blast system, but using glass bead.
The RXS900 glass bead peening systems differs from the shot peening system by having a Guyson built cyclone reclamator. This extracts everything from the base of the blast cabinet and separates out re-usable blast media from the dust and debris created by the blast process. The lighter particulates being drawn off into the dust collection unit, the heavier blast media flows down the cyclone body and into the media reservoir position above the pressure pot ready for re-use.
On exiting the glass bead peening system the robot transfers the processed components to the right hand unloading carousel, ready for the operator to remove. The operator is not able to access the blast area as both it and the robot are encased in a safety enclosure fitted with fortress interlocks. Once both systems are fully loaded, a continuous production run of one part in and one part out follows.
At the completion of the batch set the un-load carousel indexes, presenting the work pieces to the operator. Simultaneously for traceability, batch processing records are written to an SD card or network computer to document and record the status of each piece within the batch.
Prospective user of Guyson automated blast systems are encouraged to submit sample components for free feasibility testing to the company's extensive development test centre located in Skipton, England. Please contact Guyson's customer service department now to arrange free blast trials on your components, prove the process and make recommendations on the most suitable blast system for you - call +44 (0)1756 799911 or email info@guyson.co.uk
Guyson International Limited
Snaygill Industrial Estate, Keighley Road,
SKIPTON, North Yorkshire, England BD23 2QR
About Guyson
Guyson International Limited is a privately owned family company with a world-wide reputation for excellence in the design and manufacture of blast finishing, spray wash and ultrasonic cleaning equipment. Formed over eighty years ago, the company is registered to BS EN ISO 9001: 2015 and BS OHSAS 18001:2007, and its head office is located at Skipton, North Yorkshire, in the north of England. Guyson has four international subsidiary companies: Guyson Corporation of the USA, located in Saratoga Springs, New York State; Guyson SA, situated near Paris, France; Guyson Sdn Bhd in Penang, Malaysia; and Guyson CN, in Wuxi, Jiangsu Province, China.
This release was published on openPR.
Permanent link to this press release:
Copy
Please set a link in the press area of your homepage to this press release on openPR. openPR disclaims liability for any content contained in this release.
You can edit or delete your press release Guyson Robot Loaded Shot Peening Automation With Traceability here
News-ID: 1975894 • Views: …
More Releases from Guyson International Ltd
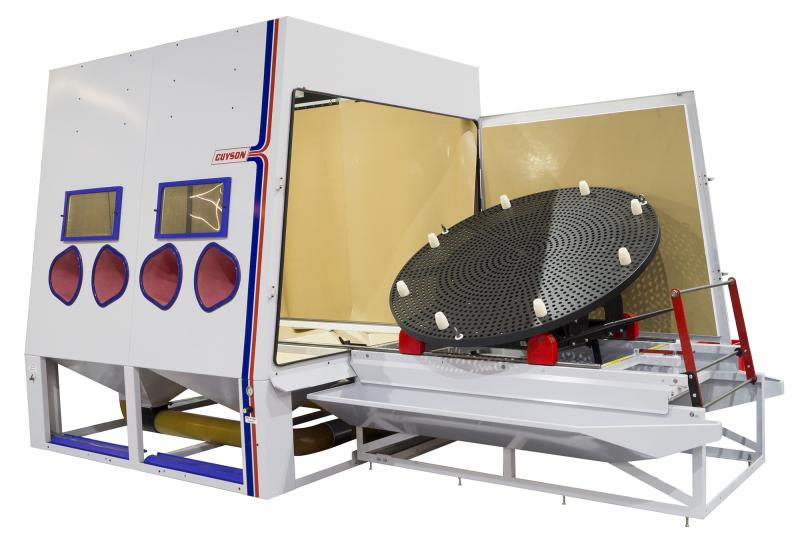
Extra-Large Blast Machine for Blast Etching Aerospace Rings
Guyson International, the UK's foremost industrial finishing equipment manufacturer, has installed a Guyson Euroblast® 2-metre PF (Pressure Fed) blast system into a division of a leading European aerospace company. The extra-large blast cabinet is used to deliver a uniform etched key surface on a range of machined circular aluminium rings prior to bonding.
After blast trails performed at the company's Skipton demonstration centre, a Euroblast 2-metre PF blast system (2.1…
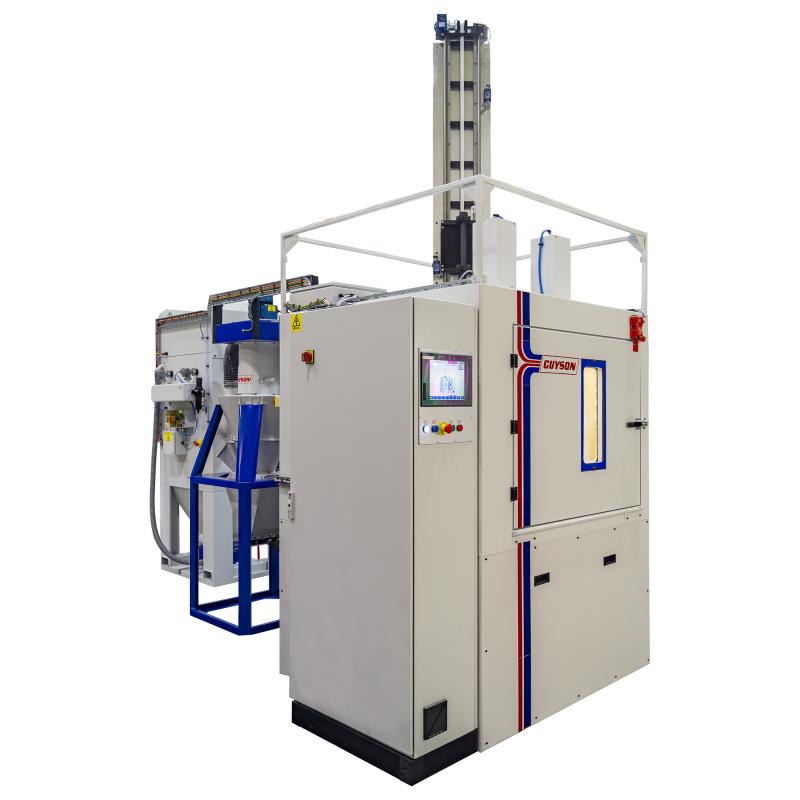
Guyson Twin Spindle Blast Machine for Etching Tubular Components
Guyson International, the UK's leading manufacturer of industrial finishing equipment, has recently manufactured and installed into a UK manufacturing company an automated Multiblast RSB twin spindle blast system for externally blast etching various sizes of tubular components. This new blast system incorporates two rotating blast stations with matching top clamps, to hold the product securely, whilst two vertically traversing blast guns produce a uniform blast etch finish over the length…
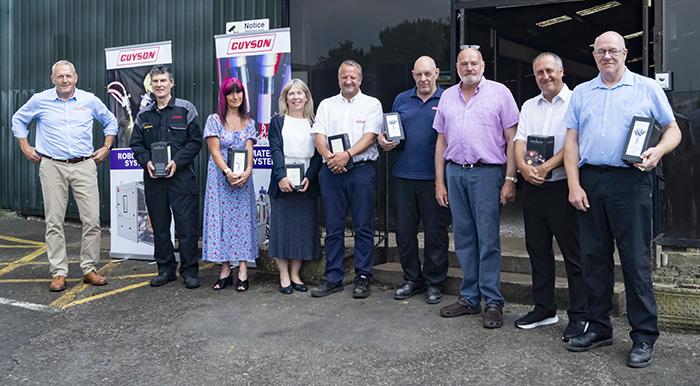
Guyson Staff Clock-Up 180 Years!
At Guyson International's Skipton headquarters, Monday 15th August saw rain, much needed, and celebrations, much deserved. Employees from the company's blast and wash division gathered outside to congratulate seven employees who were awarded long service awards. And between them amassed a total of 180 years of service at Guyson, with one, Keith Miller celebrating 50 years of service.
In typical unpredictable UK weather, after so many days of bright hot sunshine,…
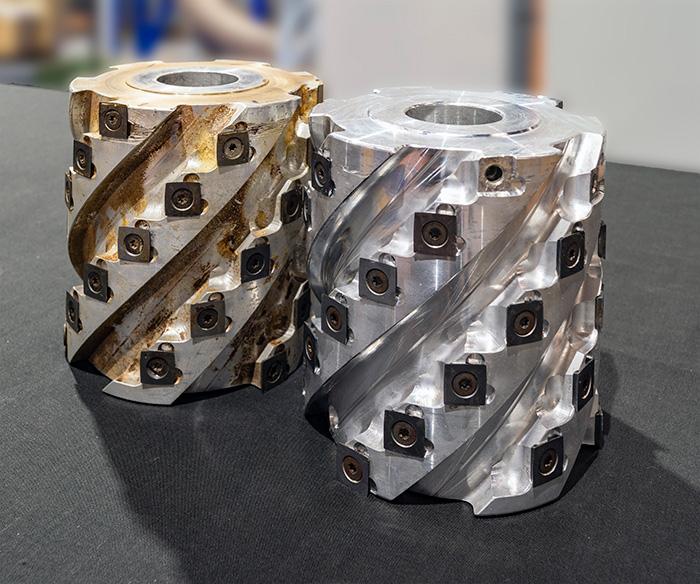
Guyson Equipment Cleans and Maintains Planing and Woodcutting Tools
Guyson International, one of the UK's leading manufacturers of industrial finishing equipment, recently delivered a KS450 ultrasonic cleaning tank and a Formula 1200 benchtop bead blast cabinet to RHW (R H Wilson (Lakes) Ltd.) of Kirkby Stephen, a leading timber importer and supplier, for cleaning and maintaining their wood cutting and planing tools.
The problem was how best to clean 'helical planer blocks' to remove a build-up of pitch, sap, resin…
More Releases for RXS900
New Guyson ‘Automated Blast Products’ Brochure
For the Autumn season Guyson International, the UK’s foremost industrial finishing equipment manufacturer, have issued a brand new ‘Automated Blast Products’ brochure that showcases its comprehensive range of ‘automated’ blast systems. Through this twelve page brochure Guyson aims to show that, as manufacturing moves to greater levels of automation, control and integration, their range of automated blast systems are designed to fully integrate with customers’ production systems and provide the…